Yeehaw! I anticipated this step all day. I had originally planned to use Dowelmax to join these pieces because I was more comfy with the jig and this has to align perfect. I then though, phooey! I'll use Domino and give it a good test drive.
The first picture shows the Festool Domino fitted with the Trim stop. This fitting allows you to "center or off-set the Domino joiner on narrow work pieces for perfect positioning."

HA! If anyone can screw this up, I can! I defy a tool company to make a jig that I can't find a way to ignore the instructions and eventually misuse....
Well, as you can see in the background, I had to get the instructions out. I couldn't figure out how to put the trimstop on the Domino. After about 4 seconds of looking at a picture, banging me head into the headstock on my lathe in self disgust, I fit the trimstop on and centred the unit to the test piece that I had measured and marked, and made a test cut.
After making the first cut, I just stuffed each piece into the the trimstop and cut the remaining 15 mortises. Clarity of thought might have led me to take my time and measure each one to ensure that I was going to end up with the right alignment in the end, but trust tthe tool, I always say. Sometimes, I end up being the "tool."
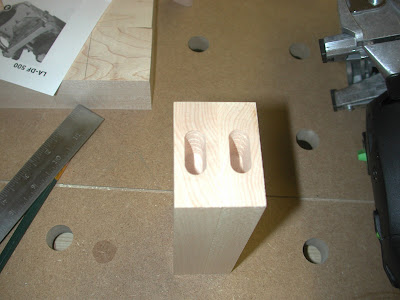
They look okay, but time will tell. There is another essential step or two to see if I can pull this off. As you can see, I decided to put two (2) dominos in each joint just to really test the limits of measurement error or success.
Now, when I went to measure and mark where I wanted the ajoining mortises on the tressel base and top, the indexing pins on the Domino were too close to the edge. I tossed on the outrigger attachment and found to my horror that I was in the "in between zone." Crap! Well, just move where you want the mortises. Right? That would be too easy. Lets find another way to index. I started thinking, "What would Dowelmax do?"
I didn't really think that, but the indexing rod for Dowelmax was sitting on the bench and I just happened to pick it up.
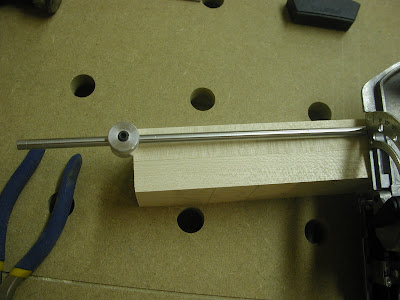
I lined up the Domino on the first cut, set the indexing rod, and proceeded to cut the remaining 15 matching mortises in the tressel base and tops. This is NOT going to fit. No way, no how. But, I press on!
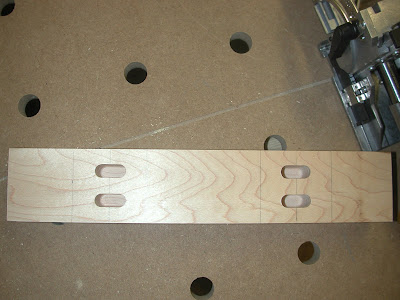
Just when I must be looking like a genius to everyone reading this, my humility knows no boundries. So I have therefore included a video of me trying to use the darn indexing rod. I mean, this is really Keystone Cops stuff. In my defence, however, if I held the Domino with my right hand, and the indexing bar with my left...even with the opposite side cross-over maneuver, then this entire process goes REALLY easy...I may remember that for next time...may.
Well, they look pretty good to me. They still have to fit though. You see, back in the beginning, I forgot to mention how I had chosen to make this EVEN MORE difficult. I could have milled the tressel base and legs to exact dimensions. Then just set the fence on Domino (hereafter affectionately named, Lucille (BB King Joke).) Instead I wanted a reveal on every leg. I'm going to make this so there is not a popsicle's chance in the Bayou of working....this involved some test cuts and measuring on some scrap...it took about 20 minutes to get things setup where I thought they were pretty good.

Well, so far so good, eh? (I'm Canadian)
I didn't get too excited, as anyone that has made a piece with slats or spindles knows, the big gal hasn't sung yet...I still have to lined up the ajoining piece of tressel top. I'm admittedly equally excited and nervous at this point.
I put glue on (more than the picture shows) and drove the pieces together with my handy dandy mallet and a piece of scrap wood. This little endeavour met with a knock on the shop door and a rather annoyed look from my wife...kids sleeping...banging...all that...yada yada yada...I'm on a role...I'll fix the damage to the upper two floors in a second.
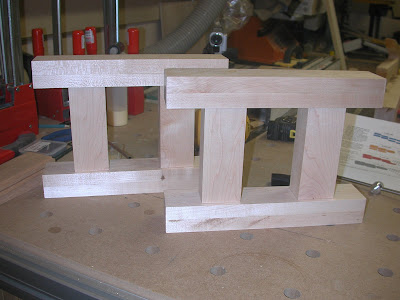
Well, nobody was as shocked as I. They both fit. I tossed a couple of K-bodies on them and left the shop for the night to tell my imaginary friends of my exploits of precision and design...or blind assed luck...depends on how well you know me!
The project forges forward!